You can have today’s best DOT compliant lighting instead of the 1980s pickup truck technology.
As the new owner of a 1997 Prevost XLV coach in 2016 there was so much to learn, love, and respect about the commercial Prevost chassis designed with a 3 million mile usable life. The first drive at night demonstrated one of the deficiencies that defies Prevost’s otherwise valid claim that they build “The Ultimate Experience”.
Prevost sourced the 1987 Ford F-150 pickup truck headlight for the Prevost XLs which were a proven halogen lamp based headlight solution with both low and high beams in a single reflector and lens housing.
Fast Forwarding 30 Years
Vehicles in the 1990s were still equipped with cassette tape players which were being replaced by CD players. Today music is streamed or downloaded through popular music services. The lighting technology of the past 30 years has migrated from Halogen to HID and now LED which uses significantly less power while producing less heat than previous technologies.
I will post the data sources (independent testing by universities) in a future update, but the combined distance of a Prevost to stop from 45 miles per hour to zero along with the typical reaction time for a driver to react to a situation and apply full braking power equates to approximately 286 linear feet. Again, this is from 45 miles per hour – not the 65, 70, or 75 miles per hour posted on today’s interstates. I am conducting my own independent testing but I am quite confident the light output of the original Ford headlight would be barely usable at 286 linear feet which means I, like many others, was driving at or beyond the limits of the headlights’ ability to illuminate the road and its hazards ahead.
I began my research by searching for the best headlight that could fit in the space afforded by the Prevost headlight bezel and maintained the aspect ratio of the rectangular opening to integrate with the original aesthetic design. The nearest headlight size to fit in and fill the space is a 5″ x 7″. The undisputed leader in DOT compliant LED lighting retrofits is JW Speaker based in Wisconsin.
JW Speaker’s 8900 and 8910 (heated lens version) headlights were a perfect solution, but one cannot simply order these and bolt them to the front of the Prevost. It requires a custom-fabricated solution. The compound curves of the front grill and bezel combined with the organic shapes of the recess behind the headlights makes it difficult to design a compatible solution.
My first attempt was a one-off solution using all stainless steel that I hand-fabricated and fit to the coach using tools found in a typical home shop. It was laborious (over 100 hours) and would be difficult to repeat consistently. Even my one-off had character flaws only I would recognize. However, it worked. It worked very well. I drove cross-country on multiple trips racking up over 10,000 miles of night driving. I enjoy driving at night, but only when eye fatigue isn’t a factor.
The support from the Prevost community was unexpected. I received enough positive feedback and requests for me to build a kit version of it that I finally had to give it serious consideration. To make it affordable, repeatable, and the highest quality I needed some professional assistance.
Through the help of Weller Racing in Chandler, Arizona the entire front headlight area was scanned with a laser to create a perfect 3D model (or “point cloud”). This 3D model allows for precision design and engineering of any products including automotive parts. The 3D scan led to three test-fits of the pre-production mock-up to simply fine-tune the tolerances.
This product has very small gaps – far smaller than the factory standards. To make sure each owner can obtain a perfect fit, the product can be adjusted on two different axis. The image below shows the adjustability in both vertical and horizontal axis to adjust the position of the headlight within the bezel. We also added a “fourth leg” which provides additional support against the interior recess of the Prevost headlight area that provides greater stability than the original installation which relied on only three legs of support.
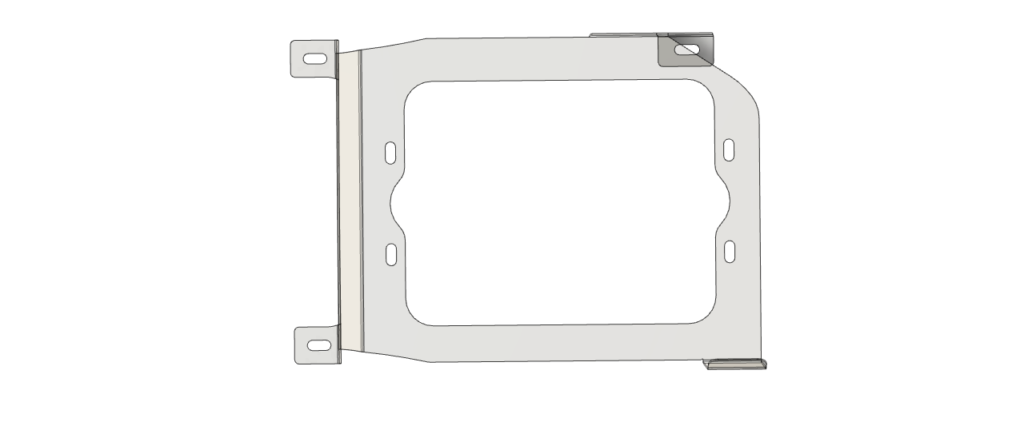
The center opening shown above supports the commercial grade 5″ x 7″ headlight bucket which is made of composite material and has integral headlight adjustment for beam angle in horizontal and vertical planes. This is different adjustability as it is for the headlight beam throw and not the centering of the headlight inside the factory bezel that surrounds the headlight and turn signal.
All fabricated materials are 304 Stainless Steel just like the Prevost panels. The sub-assembly is 16 ga. The finished exterior trim fascia is 18 ga. with a #8 factor polish (also known as “mirror-finish”). It will be more reflective than any coach that has been driven for the past 30 years. You could literally shave in the reflection of the mirror. All hardware, wherever possible, is stainless steel. The goal is for this product to last the life of the coach that remains. Should a 5″ x 7″ need replacement in the future it is an easy roadside swap but the life of LED is markedly longer than any halogen bulbs.
JW Speaker backs all of the non-heated lights with a 5-year warranty and the heated lens versions with a 2-year warranty. Their rate of warranty returns is very small. Be warned that there are multiple knock-offs on the market built overseas. If you try to find photometrics on those lights you will find them conveniently missing We are an authorized reseller of the JW Speaker product from an authorized distributor.
Every product purchased for this kit, including the custom electrical harness we fabricate is sourced from US based factories. All connectors and electrical wiring meet or exceed DOT and Prevost standards.
A series of installation instructions and videos are being developed to help with the installation. Any coach owner that carries a toolbox on board should be able to remove the bezels with a screwdriver, remove the factory headlights with a socket wrench, and cut the old headlight connector off leaving three wires per side (low beam, high beam, and ground). The harness will be shipped ready for splicing to the factory wiring and equipped with both marine grade crimp/heat shrink connectors and Posi-Lock products so you can choose which method you prefer. Additional layer of heat shrink will be provided for double-protection. This method will outlast the factory method of terminating at the headlight connector you cut off.
This is an afternoon project that could take as little as two hours including alignment once it is dark. For additional questions, please email or call me:
matt@prevostLEDupgrade.com
602.620.2289 (mobile)